ex GST and Shipping
A fabrication guide to Kennedy Nolan's designs
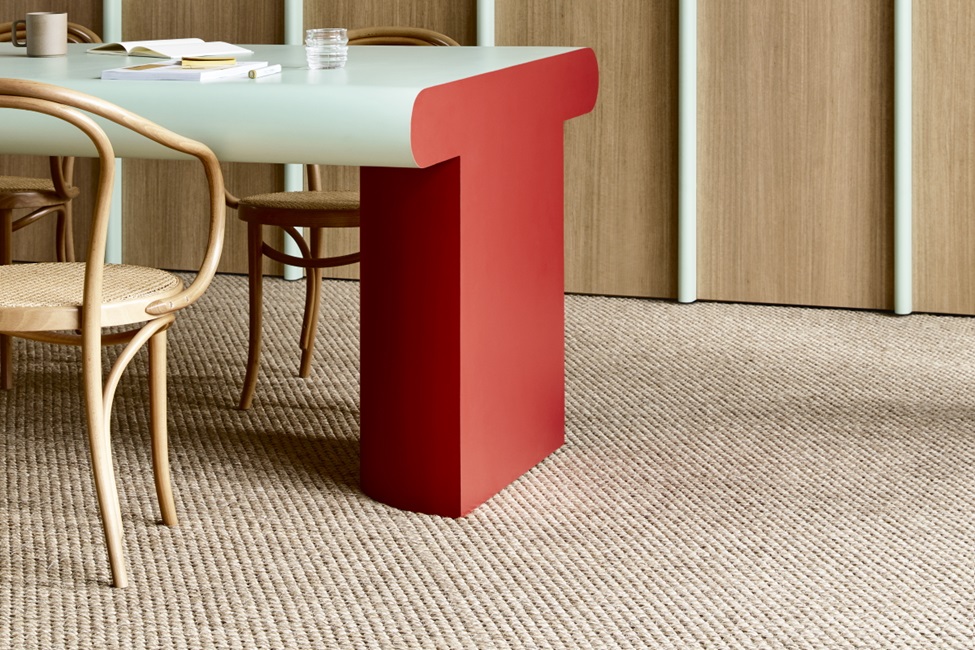
With two beautiful designs inspired by the versatility of Laminex® laminate, it was the job of an experienced fabricator to bring them to reality.
We talk a lot about the creativity of architects and designers, but the ingenuity of the fabricators who build their designs is often overlooked. Andy Joachim, Design and Fabrication Manager at Evolve Interiors, was responsible for building two major elements from Kennedy Nolan's design collaboration with Laminex – the meeting table in Workplace and the island bench in the Expansive Kitchen – and we asked him how it was done.
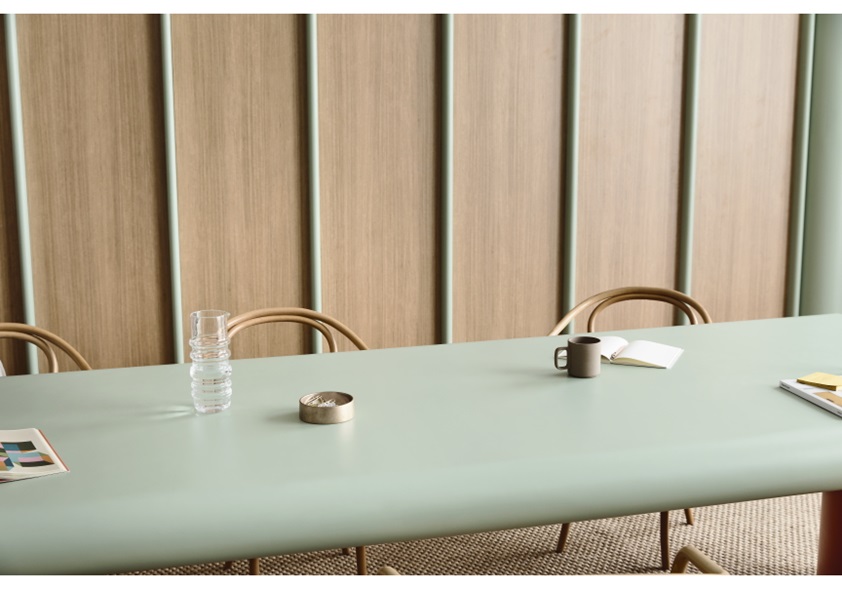
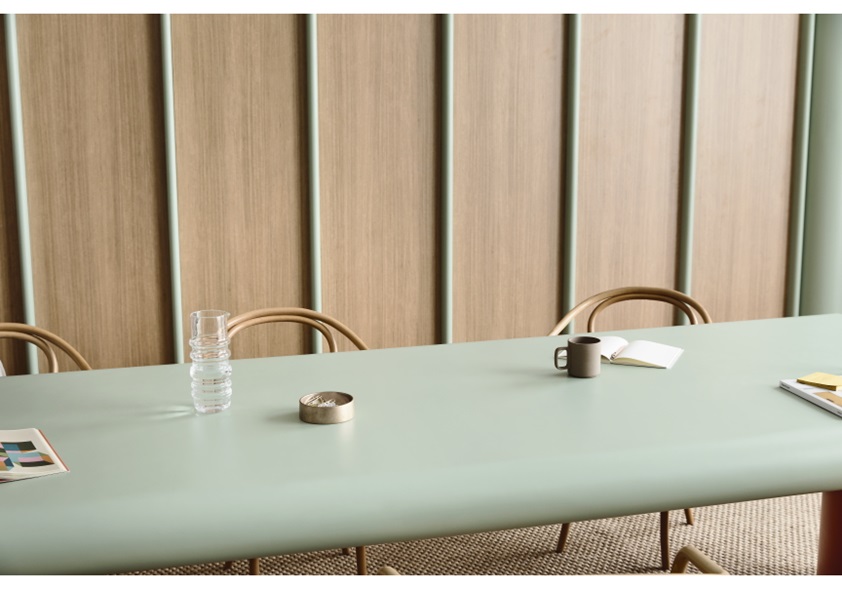
Fabricating the meeting table for the Workplace
Joachim started with the meeting table's top section, building a skeleton with MDF ribs that were half-overlapped at the centre, for maximum structural integrity, and encasing it in 9mm-thick Trade Essentials Bending Plywood. "The radius of the tabletop was a little smaller than the minimum recommended for the plywood," Joachim explains, "but we did some testing and found that, if we wet it, got the iron on it and steamed the ply, we could achieve the desired curve." Following this method, he "screwed and glued" the plywood in place, starting on the flat underside of the tabletop and working around the curve. The screw holes were filled and the entire tabletop sanded back.


The two drum-shaped legs were also fabricated from MDF and Bending Plywood, and then all three components were screwed together, ready for Laminex laminate in Enamel and Pillarbox. To ensure that the table appeared as seamless as possible, with edges and joins concealed, the order that the surfaces were laminated in was carefully considered: first, the curved section of the legs; then the flat ends; and finally the tabletop.
Please note that Laminex Enamel has been discontinued; recommended alternatives for this décor are Laminex Bayleaf or Laminex Spinifex.
Fabricating the island bench for the Expansive Kitchen
The legs for the island bench were fabricated in a similar fashion to the meeting table's, from MDF and Bending Plywood, but the benchtop demanded a whole new approach. Its structure was a relatively simple melamine box, but Kennedy Nolan's design required high-pressure laminate (HPL) in Laminex Paper Bark and Laminex French Cream to be laid in a pattern of just-touching circles. The HPL had to be cut with great precision on the CNC machine, and Joachim's concern was that it would move around during the process. "Our solution was to spray contact adhesive onto the bottom of the laminate sheet and let it dry, so it'd be a bit stickier on the bed of the CNC," he says. "We then put another sheet on top to keep it in place, minimising tear-out at that fine point in the pattern."
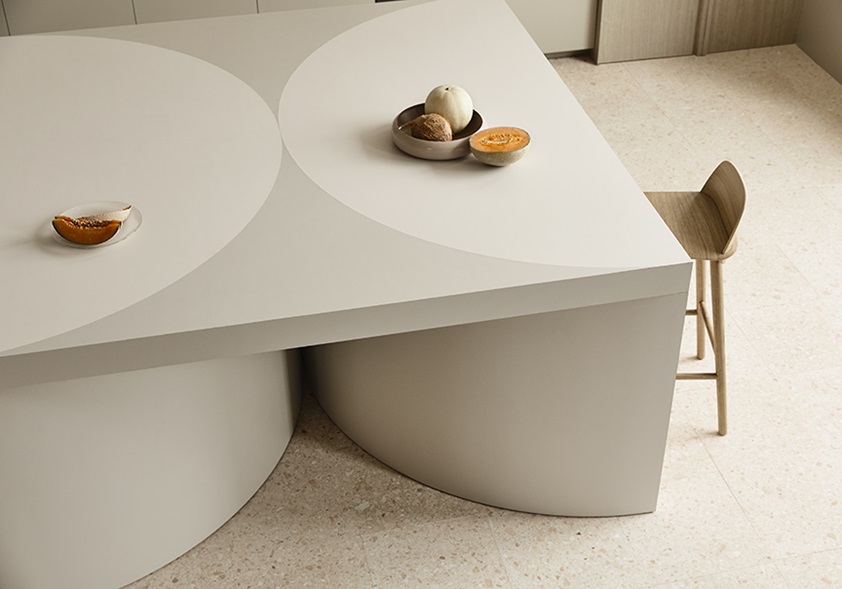
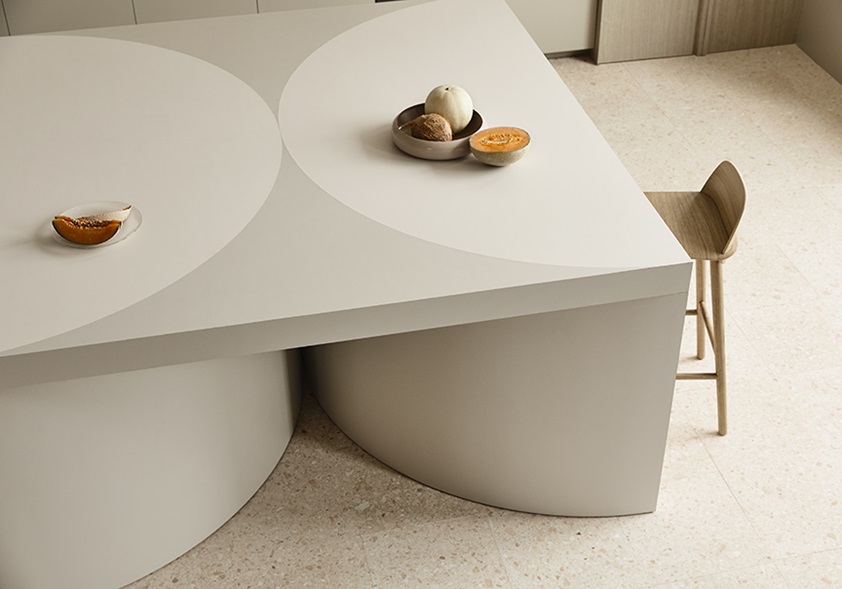
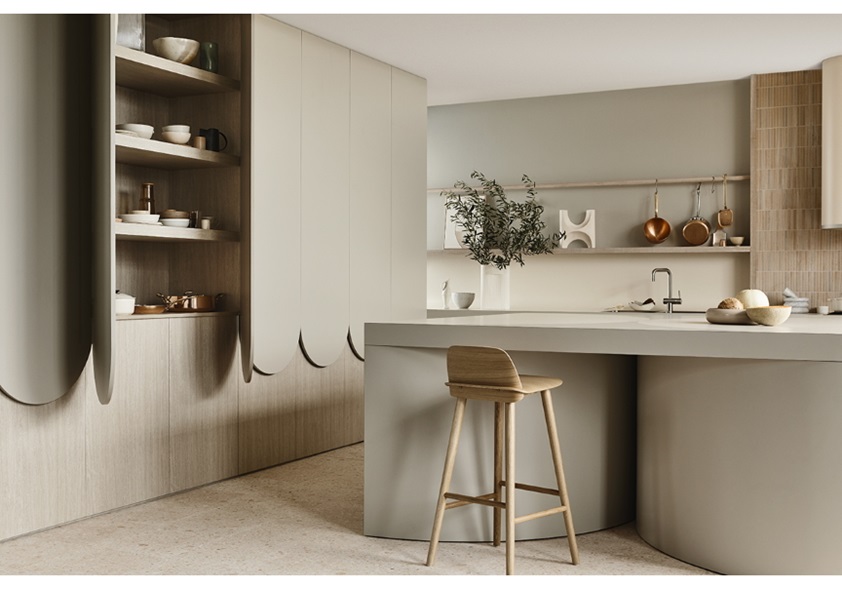
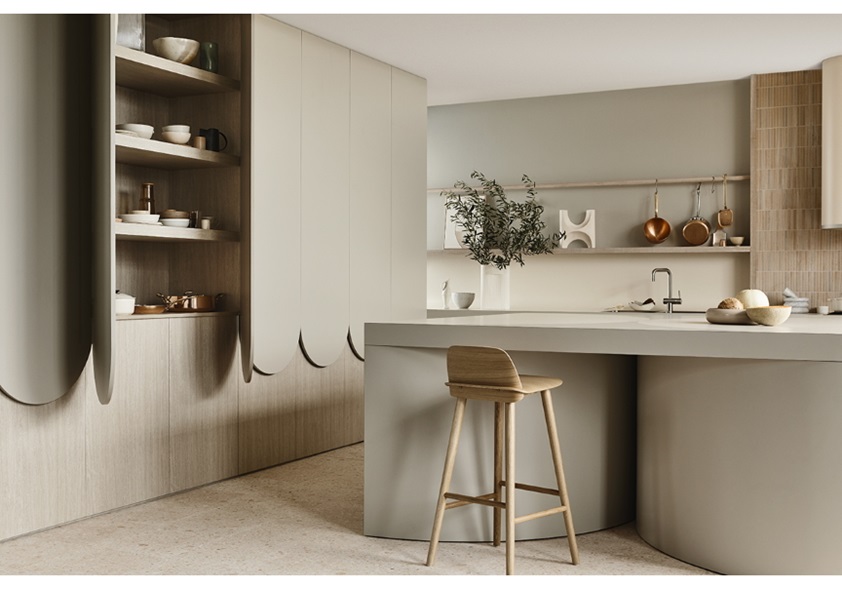
The resulting four pieces of HPL were joined with masking tape to create a single sheet, ready to be adhered to the substrate, but even then the process was exacting. As Joachim points out, "Once you've sprayed the contact onto the bottom of the sheet, and onto the substrate, you only get one shot!" Ribs were placed across the benchtop, with the HPL on top, each corner was carefully lined up, and then the supports were removed one by one as the HPL was laid down. As you can see in the photographs here, the result is perfect! Reflecting on the two projects, Joachim says "We work with a lot of different materials, but when a design moves away from the stock standard square edges and has curved surfaces, the best solution is laminate."
Workplace decors
Tower joinery: Laminex Sublime Teak and Laminex Enamel
Table and shelf: Laminex Enamel and Laminex Pillarbox
Expansive Kitchen decors
Island Bench: Laminex French Cream and Laminex Paper BarkTower Scallop Cabinetry and Internal Cabinetry: Laminex Paperbark and Laminex Whitewashed Oak
Rear benchtop, curved splashback and rangehood: Laminex French Cream
Rear cabinetry: Laminex Paperbark
Contributors
Architects: Kennedy Nolan
Creative Direction: Ortolan
Photographer: Derek Swalwell
Stylist: Natalie James
Editorial Consultant: Infinite Shapes
NEW
Laminex Specifier Accounts
Sign up for exclusive access to large-format samples, higher sample quantities and the latest product news